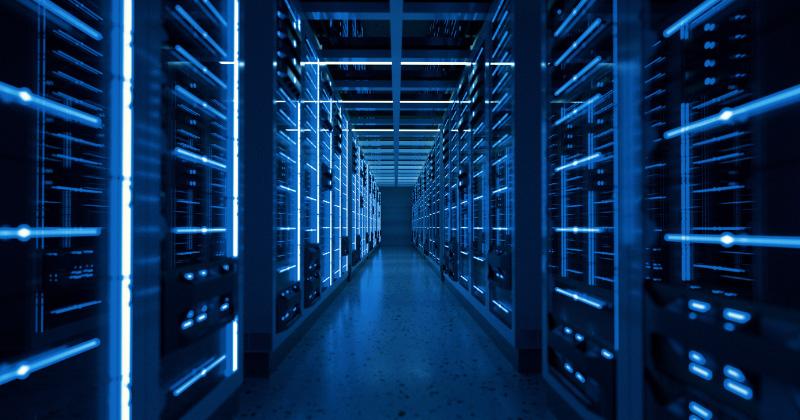
Microchip Reveals CAN FD System Basis Chip in Tiny Footprint
Microchip Technology recently announced its new ATA650X series, a compact CAN FD system-basis chip (SBC) designed for automotive and industrial systems.
The ATA650x CAN FD SBC for space-constrained applications. Image (modified) used courtesy of Microchip
The ATA650X combines a high-speed CAN FD transceiver with a low-dropout voltage regulator to enable faster, more reliable communication across electronic control units (ECUs).
A New CAN FD System Basis Chip
Integrating a CAN FD transceiver and a 5-V/150-mA low-dropout voltage regulator, the ATA650X series (datasheet linked) supports data rates up to 8 Mbit/s and adheres to ISO 11898-2:2024 and SAE J2962-2 standards. The voltage regulator provides an output voltage with a precision of ±2% and a dropout voltage of up to 750 mV at 150-mA loads. It delivers a maximum current of 150 mA, supplying power to the transceiver, microcontroller, and external components.
Designed for harsh conditions, the ATA650X can operate across a wide temperature range of -40°C to +150°C and with supply voltages from 4.5 V to 28 V, handling transients up to 40 V. Microchip designed the CANH and CANL pins for high reliability, withstanding transient voltages of ±150 V and offering ESD protection up to ±6 kV (IEC 61000-4-2).
ATA650x simplified block diagram. Image used courtesy of Microchip
From a power perspective, the device supports multiple operating modes, including Normal, Sleep, Standby, and Receive Only modes and ISO 11898-2-compliant wake-up functionality. In Sleep mode, the device achieves a low current consumption of 15 µA at 25°C. In normal operating mode, the internal transceiver consumes 50 mA during a dominant bus state, leaving 100 mA from the LDO available for external loads.
CAN and CAN FD
The automotive industry has long relied on Controller Area Network (CAN) systems to manage in-vehicle communication and ensure reliable data exchange among electronic control units (ECUs). However, traditional CAN protocols, with a maximum data rate of 1 Mbit/s and payloads of 8 bytes per frame, have struggled to keep pace with the increasing demands of modern vehicle architectures. Technology such as advanced driver assistance systems (ADAS), over-the-air updates, and real-time diagnostics require significantly higher bandwidth, faster communication rates, and improved efficiency.
CAN FD (flexible data rate) was developed to address these challenges and has become a key to next-generation automotive communication. Offering data rates of up to 8 Mbit/s and payloads of up to 64 bytes per frame, CAN FD significantly increases the throughput and efficiency of in-vehicle networks. Meanwhile, the flexible data rate within a single frame reduces latency and optimizes bandwidth usage. Moreover, CAN FD incorporates advanced error detection mechanisms that improve communication integrity and reliability in safety-critical applications.
A CAN FD frame. Image used courtesy of National Instruments
CAN FD also maintains backward compatibility with classical CAN, allowing manufacturers to upgrade existing networks incrementally while preserving investments in legacy infrastructure. This flexibility also helps automotive OEMs and suppliers transition to more advanced architectures as the automotive industry progresses toward fully autonomous and connected vehicles.
CAN FD for Automotive Progress
As vehicles evolve toward higher levels of connectivity and automation, the need for robust, high-speed communication protocols becomes critical. CAN FD, with its increased data rates and payload capacity, offers a scalable and reliable solution to meet these demands. Microchip’s ATA650X series, built to leverage the strengths of CAN FD, is now available for purchase in production quantities.