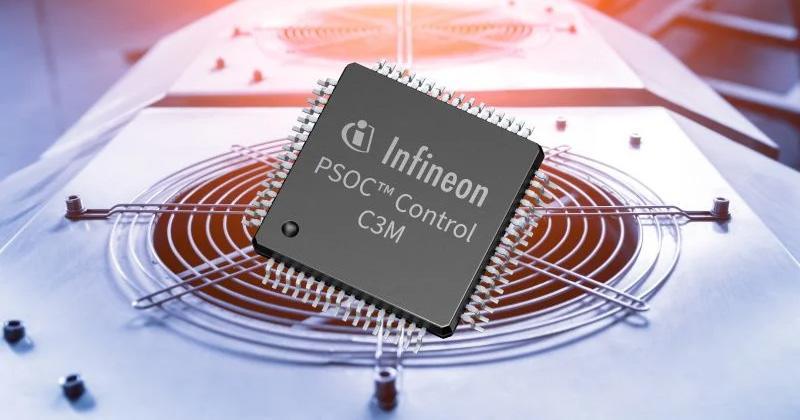
Key Considerations When Specifying Soft Starters for Industrial Motor Applications
Many industrial applications like conveyors, pumps, automatic doors, overhead traveling cranes, and so on use asynchronous motors that run at constant speeds, do not need high levels of startup torque, and can benefit from the simplicity of using motor soft starters. Soft starters protect motors and mechanical system components from shock, increase operating life, reduce peak electrical demand to minimize energy consumption, and can improve operator safety.
There is a range of choices for motor starters, and to get the maximum benefit and operating life, they must be specified appropriately. Some of the basic questions include:
Is the application for a UL/NEMA or IEC environment?
Is the motor single-phase or three-phase?
What is the motor’s voltage, power level, and full load amps?
Does the application need adjustable parameters like starting and deceleration times and unjamming torque levels?
What communications protocol will be used?
Beyond the basics, there are important considerations related to demands for cybersecurity, the need for coordinated motor starters as defined in the International Electrotechnical Commission (IEC) 60947-4-1 and 60947-6-2 standards, overload or thermal protection and motor classes as defined in American National Standards Institute (ANSI) 49 standard for “machine or transformer thermal relay / thermal overload,” and a wide range of additional protection options.
This article briefly reviews the basics when selecting motor soft starters before presenting a more detailed review of advanced features like coordinated motor starter considerations, protection features, cybersecurity needs, and exemplary soft starters from Schneider Electric.
The basics
There are differences between motor specifications used in a UL/NEMA versus an IEC environment. It is essential to know the location of the application; NEMA applies in North America, while IEC is used in Europe and other regions. Overall, NEMA allows more variation in several specifications, while IEC tends to have tighter tolerances.
For example, on NEMA nameplates, the motor’s rated load current has a tolerance of ±10%, while IEC nameplates do not include a load current tolerance. On NEMA motors, the rated voltage is stated with a ±10% tolerance, and IEC motors have a ±5% tolerance. NEMA and IEC use different rating systems to define the torque-speed profiles of motors and the motor service factor.
Other important considerations include whether the motor will be powered with single-phase or three-phase power, and what the motor’s specific voltage, power, and full load amps will be. Some applications require adjustable starting or deceleration times. What are the motor characteristics if the motor shaft is jammed under running conditions? Can the starter handle the increased current draw?
It is also necessary to look at the connectivity requirements of the application. Simple motor starters have no connectivity. Some soft starters are designed to handle a single protocol like Modbus. Others can have choices like Profinet, Modbus, Ethernet/IP, CANopen, etc.
Coordinated motor starters
Electrical faults in motor controllers like soft starters can create safety concerns. Addressing faults takes a variety of protection devices like fuses or circuit breakers. The IEC has developed standards and testing procedures to ensure safety is achieved through “coordination” of the various devices.
The standards require that a coordinated starter be tested under extreme fault conditions. The device is needed to quickly clear the fault without risk to the operator or damage to the motor installation. IEC 60947-4-1 details two types of coordination: Type I and Type II. Type III coordination is detailed in IEC 60947-6-1. The three types of coordination are defined as:
Type I – is basic coordination. It is low cost and is appropriate when machine uptime is not a priority. Type I does not support continuity of operation. Once implemented, replacement of the starter is recommended before restarting the motor.
Type II – is a higher-performance solution. It supports reduced downtime and does not require replacement of the starter after a fault. The starter is required to be ready for immediate reuse after a fault following an inspection. Simple “repairs” are allowed; for example, contacts may become welded but can be quickly separated.
Type III – provides the highest performance. After a fault, there is no damage to the equipment, and the starter must be immediately able to restart the motor with no resetting, inspection, or repairs. Type III coordination is designed to support mission-critical applications.
Overload trip classes
In addition to defining coordination types for protection circuits, IEC 60947-4-1 (and IEC 60947-6-2 along with ANSI 49) defines trip classes for motor overload and thermal protection. Trip classes define the time needed for a protective relay to trip when the current rises to 7.2 times the rated current (Ir). The trip curve of the thermal protection device determines the trip class. The higher the class number, the longer the relay takes to trip; for example, Class 20 takes longer to trip than Class 10 (Figure 1).
The standard identifies four trip classes: 5, 10, 20, and 30. Those class designations correspond to the maximum tripping time. The precision of the tripping time is -20%, + 0%, as follows:
Class 5, tripping time 4 to 5 seconds
Class 10, tripping time 8 to 10 seconds
Class 20, tripping time 16 to 20 seconds
Class 30, tripping time 24 to 30 seconds
Voltage and torque control
The Altistart 22 family of soft starters from Schneider Electric support controlled starting and stopping of 4 to 400 kW (3 to 500 HP) three-phase asynchronous motors using voltage and torque control. They are designed for use in applications with class 10 motor protection. For example, model ATS22C25Q is optimized for use with pumps and fans and is rated for supply voltages from 230 to 440 Vac. It can support 75 kW motors with a supply voltage of 230 Vac and 132 kW motors if the supply voltage is 400 Vac or higher.
Starting and stopping cycles are managed using silicon-controlled rectifiers (SCRs) that control the voltage the motor sees and limit the current. Once the motor is fully started, a bypass contactor is turned on, taking the SCRs out of the circuit, and improving operating efficiency. Figure 2 below illustrates the operation of an Altistart 22 soft starter compared with an uncontrolled motor start:
Uncontrolled asynchronous motor start results in a large surge of current, Is, and a torque of Ts
Altistart 22 results in total torque range of Ts1 that depends on the current limit setting, ILt. The resistive torque of the load, Tr, must be less than the Ts1 torque, or the motor won’t start.
Starting times using Altistart 22 soft starters are defined relative to the motor protection class as follows:
Class 10, 16 seconds for a soft starter rated for the nominal motor current
Class 20, 32 seconds for a soft starter oversized by one rating level compared to the nominal motor current
Class 30, 48 seconds for a soft starter oversized by two rating levels compared to the nominal motor current
Altistart 22 soft starters are designed for applications requiring up to 350% of rated current, IcL. Larger starters must be specified for heavy-duty applications requiring higher levels of IcL. Key factors that determine the correct Altistart 22 model for a given application include:
Motor nameplate power and nominal current ratings
Operational duty cycle
Starting current capacity
Number of starts per hour
Motor thermal protection class
Ease of commissioning is an important feature of Altistart 22 soft starters, and it’s supported in several ways. For example, the integrated Modbus port enables these connections and uses:
For connection to a Modbus network, Schneider Electric’s SoMove PC software enables configuration files to be created and stored offline and quickly commissions an installation. SoMove PC software can also be used for monitoring and diagnostics purposes.
The Altistart 22 iPad App can be used to create, save, and transfer configurations from an iPad to the Altivar 22.
A remote-mount keypad can be used to enable access from outside of an enclosure.
In addition, the Altistart 22 has an integrated interface that allows a technician to change both the programming and the adjustment or monitoring parameters (Figure 3).
Torque limiting
Altistart 01 soft starters can be used as a torque limiter on starting or as a soft start/soft stop controller for asynchronous motors from 0.37 to 15 kW (0.5 to 20 HP). They are available for single-phase and three-phase motors and have integrated bypass contactors. For example, the ATS01N206RT is designed for use with motors up to 3 HP operating from a supply voltage of 460 to 480 Vac. These soft starters are designed for starting machines that don’t need a high starting torque like:
Automatic doors and gates
Belt-driven machines
Fans
Compressors
Pumps
Small cranes
The ATS01N1 models control the starting time of the motor by ramping up the voltage applied to one phase of the motor. In contrast, the ATS01N2 models control two phases of the motor power supply to limit the starting current and for deceleration. For ATS01N1 models, the starting voltage ramp time can be adjusted from 1 to 5 seconds, and the initial voltage level can be adjusted from approximately 30 to 80% of the AC line voltage level (Figure 4).
Adding cybersecurity
Applications where cybersecurity is an important consideration can turn to the ATS480 soft starters from Schneider Electric. These units have been designed according to the IEC 62443 standards delineating cybersecurity best practices for operational technology in automation and control systems.
Cybersecurity features in these soft starters protect against casual or intentional interference or attacks like unintentional information disclosures, tampering, denial of service attacks, and spoofing/elevation of privilege. Cybersecurity functions include:
User account management to enforce authorization
Enhanced cybersecurity features built in to restrict or disable ports and services
Threat intelligence to generate security-related reports
Secure boot
Cybersecurity-compliant firmware upgrade with the firmware digitally signed and only applied if the ATS480 verifies authenticity
Models are available from 3 to 900 kW. They can operate from a wide range of supply voltages. For example, model ATS480C17Y operates with three-phase supply voltages from 208 to 690 Vac (Figure 5). Depending on the duty rating of the application and the supply voltage, this unit can be used with motors rated from 37 to 160 kW. They use dynamic braking and DC injection to stop high inertia applications efficiently.