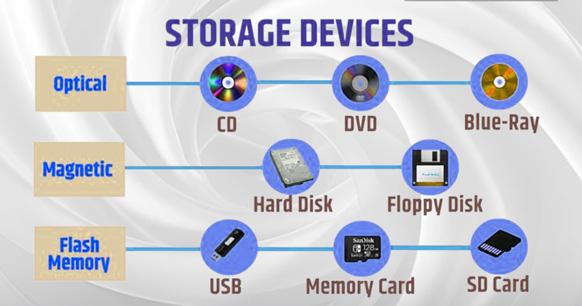
Infineon Unveils Motor Control and Power Conversion MCUs for the WBG Era
This week, Infineon Technologies introduced the PSOC Control C3 microcontroller (MCU) family to address the demands of high-performance motor control and power conversion applications. Leveraging an integrated Arm Cortex-M33 architecture, this new family offers advanced real-time control capabilities, precise system responsiveness, and robust security features.
The PSOC Control C3 MCUs can be used for HVAC, home appliances, light EV chargers, solar inverters, robotics, industrial automation, and server power supplies. Image (modified) used courtesy of Infineon Technologies and Canva Pro (used under license)
All About Circuits spoke with Steve Tateosian, Infineon's senior vice president for industrial and IoT MCUs, to learn more about the new family.
Engineered for Wide-Bandgap Power Devices
Infineon optimized the PSOC Control C3 family for use with wide-bandgap technologies such as silicon carbide (SiC) and gallium nitride (GaN). With their superior electrical properties, these materials enable higher switching frequencies and enhanced efficiency in motor control and power conversion systems. However, this performance demands fast, precise control loops—a feature the PSOC Control MCUs address with their high-speed architecture and specialized peripherals.
“The transition to wide-bandgap power devices is enabling much more efficient systems through higher switching frequencies,” Tateosian said. “That then pushes a requirement back to the MCU to control these tighter control loops at a faster speed.”
Block diagram of the PSOC Control C3.
The Main Line devices, supporting clock speeds up to 180 MHz, integrate a digital signal processor (DSP) and floating-point unit (FPU) to facilitate high-resolution control in power conversion applications. The MCUs also include high-resolution pulse-width modulators (HRPWMs) with sub-100 ps accuracy to generate the precise output waveforms needed to harness the advantages of SiC and GaN transistors.
Advanced analog processing capabilities, such as a 12-bit SAR ADC operating at 12 MSPS and parallel sampling of up to 16 channels, allow accurate real-time data capture for current and voltage measurements. These features collectively enhance system efficiency and reduce energy losses for high-speed motor drives and power supply designs.
Integration with ModusToolbox Motor Suite
An important feature of the PSOC Control platform is its compatibility with Infineon’s new ModusToolbox ecosystem, which enhances the platform with specialized tools for motor control applications. The Motor Suite provides developers with an interactive graphical interface for parameter tuning and system evaluation. By simplifying setup and debugging, the tools may accelerate the development timeline for sophisticated motor control solutions.
“With PSOC Control, we're also adding to ModusToolbox a tool called Motor Suite,” Tateosian said. “Developers can use its profiler to see what's happening in the motor, utilize oscilloscope functionality, and debug in real-time. It really takes motor control development to the next level.”
Unique features of the Motor Suite include real-time parameter monitoring and adaptive tuning capabilities. Engineers can optimize field-oriented control (FOC) algorithms or implement multi-phase PFC designs without manual recalibration. The software also supports anomaly detection and predictive maintenance by leveraging machine learning integration.
ModusToolbox also ensures compatibility across the PSOC Control portfolio. The common development environment allows engineers to scale solutions between Entry and Main Line devices while preserving code and design workflows as performance requirements evolve.
Broad Applications for the PSOC Control C3
The PSOC Control C3 family targets a wide range of applications, from industrial robotics to power conversion in renewable energy systems.
Infineon’s Main Line products, such as the PSC3P5 and PSC3M5 series, are particularly suited to high-performance designs requiring advanced control and precision. These devices can be used in solar inverters, EV chargers, and high-efficiency motor drives for home appliances and industrial systems.
The PSOC Control C3 portfolio has solutions for varying application needs.
In robotics, the PSOC Control MCUs’ real-time response capabilities unlock optimal movement and maximal energy efficiency. For home appliances, these MCUs enhance motor efficiency and durability while supporting advanced safety standards such as Class B and SIL 2 compliance. The Entry Line devices, operating at clock speeds up to 100 MHz, provide cost-effective solutions for less demanding applications, such as light electric vehicles and HVAC systems.
Furthermore, the family’s low-power operating modes, including deep sleep and hibernation down to 300 nA, extend battery life in portable applications.
Infineon Plans to Scale Portfolio Up and Down
Infineon’s PSOC Control C3 family demonstrates a forward-thinking approach to microcontroller design that aligns with trends in decarbonization and digitalization. As the market for motor control and power conversion technologies continues to grow, Infineon hopes its latest offering will provide developers with the tools and hardware necessary to stay with the times.
“The range of devices we’re launching today spans high-speed motor control, power conversion, and wide-bandgap readiness,” Tateosian said. “As these technologies grow, we plan to scale this portfolio up and down, in terms of memory and performance, to address an even wider range of applications with similar targets.”