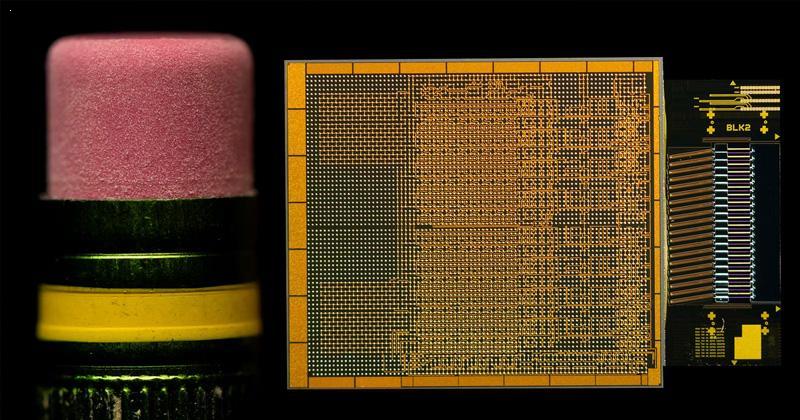
The Art of (Simulating) Electronics (With Thermistors and RTDs)
At the core of this article is the legendary book “The Art of Electronics” by Paul Horowitz and Winfield Hill, which is known worldwide by electronic engineers and published when SPICE programs were not as widespread as they are today. The purpose of this article is to demonstrate that it’s possible, with modern SPICE techniques, to reproduce many of the circuits published in the book using Vishay non-linear products.
If a poll was taken to select one book as the reference manual for experimental electronic engineers, there’s a good chance that "The Art of Electronics" by Paul Horowitz and Winfield Hill1 would be included in the top results. Back in my professional youth in the early nineties, I would admiringly contemplate the numerous exemplative circuits presented in the book’s pages, including those dedicated to circuit ideas, which closed every chapter.
Among the multitude of circuits explored in the first chapters on transistors and op amps, I found specific schematics dealing with temperature control issues and solutions. On the issues side, semiconductors like diodes and transistors experience a change in their characteristics due to power dissipation and ambient temperature variations. On the solutions side, NTC thermistors and resistance temperature detectors (RTDs) have long been used for temperature sensing, control, and compensation in order to address these potential thermal problems.
What’s changed since 1990 is that the use of SPICE simulation software has become widespread in the world of electronic engineers, and more recently, it has been joined by thermal evaluation software. LTspice® XVII, for example, has delivered advancements in thermal evaluation with tools like SOATHERM2. Recently, it occurred to me that it would be interesting to simulate the circuits in “The Art of Electronics” that deal with thermal aspects and complement them with dynamic SPICE models for temperature sensors, while including thermal models for heating elements and bipolar/MOS transistors.
The main advantage of such simulations is that inside a unique software, the original electronic circuit is on one side, and the thermal circuit with closed thermal loops is on the other. The temperature of the heated object (room or oven) can be fed back directly to the sensor, allowing for complete thermal electronic co-simulations in the cadre of one software: LTspice XVII. But before doing all this, the proper models are needed. Fortunately, LTspice is the tool for the adept DIYer.
We’ll begin with the temperature compensation of a simple amplifier stage based on an NPN bipolar transistor3. Figure 1a presents a simple circuit in which we evaluate the variation in temperature of the 2SC4102’s collector at various currents (Figure 1b).
We can see that the temperature dependence (static temperature TEMP) of the transistor is well modeled. While self-heating is not considered, a special command (pointer-alt key) can be used to represent the dissipated power. As temperature increases, the voltage base/emitter decreases, and the collector current and power increase. So why not try to include these effects in the LTspice modeling, taking into account the self-heating due to power dissipation, as shown in Figure 2? This makes it possible to build a new device: an NPN transistor with a power output (HEAT pin).Remarkably, adjusting the dI and dVBE1 parameters (which can be seen in Figure 2) to the 2SC4102’s intrinsic NPN characteristics already incorporated in LTspice XVII allows the supplementary drifts due to self-heating to be taken into account. Let’s simulate the collector current of the circuit in Figure 1a for two values of TEMP temperature (25°C and 150°C). Then, let’s compare these two curves with the current collector of the circuit in Figure 3a, where our thermal NPN is mounted with a heatsink that can dissipate at 25°C/W. The component temperature (now defined by the voltage at the HEAT pin) remains at 25°C for low VBE, and as the collector current increases, it ends up around 150°C. The green curve (Figure 3b), obtained with the thermal model is close to the static characteristic with TEMP = 25°C, then joins the characteristics with TEMP = 150°C at full dissipation.
We are now at a stage where we can simulate a transient in which an amplifier stage NPN transistor is dissipating heat and communicating it to a heatsink, then to the NTCS0805 thermistor8, which will be used to keep the current from getting out of control. This current stabilization can, of course, be compared with the same circuit without thermistor compensation (Figures 4a and 4b).
The second circuit taken out of “The Art of Electronics”4 is a thermostat for heating control (Figure 5a). This circuit is so fundamental that it can still be found in the 2015 edition of the book. My LTspice simulation is completed with the Vishay NTCLE203E3103SB0 thermistor model6 and a thermal circuit representing the room or oven to heat, connected to the ambient external temperature via the thermal resistance, and to the ground via a capacitor representing the thermal mass. The way this circuit works is described extensively in “The Art of Electronics”3, so I won’t write anything about it here. Figure 5b represents the waveforms of the delivered power to the room (or oven) and the temperature variations of the different elements. It shows that the temperature control works perfectly, whatever the external temperature variations or set temperature (50°C, 75°C, or 100°C).
The third and last example is a proposed schematic for a fast logarithmic converter with a particular temperature compensation performed by a resistor with a +0.4 %/°C temperature coefficient5. This was the perfect opportunity to introduce full SPICE models for similar temperature-dependent resistors (PTS surface-mount from Vishay7). A log converter device is used in all circuits performing dB conversion. The conversion is based on the proportionality between the NPN transistor base/emitter voltage and the logarithm of the collector current. But at the same time, it depends on temperature. And that is the reason for the presence of an RTD, which depends linearly on temperature. Figure 6a shows two circuits: one with an RTD connected between the base of Q2 and the ground (circuit above) and its equivalent with a fixed resistor (circuit under).
Figure 6b represents the output voltages of both log converters as a function of the input voltage. The blue curve is the stabilized one (upper circuit Vout1), while the green curve is the non-stabilized output (Vout2).
What I did in this article was simply prove retrospectively, via electronic simulation, that these bright design ideas really work. At first sight, they could seem a bit unnecessary. However, one should think about the hours of trial and error that were consumed during the purchase of the circuit’s parts, building schematics, and error-proofing before the finalization of these designs.
The conception of an electronic circuit does not necessarily require electronic simulation. It’s not electronic simulation that will give you the bright idea for a circuit design either. However, with the models available now, including some thermal aspects, LTspice simulation can help you test your new circuit ideas on the spot with nearly no cost or delays. Finally, it will allow you to finalize your design faster, as the first runs will now become virtual, eliminating hours of tedious trial and error.