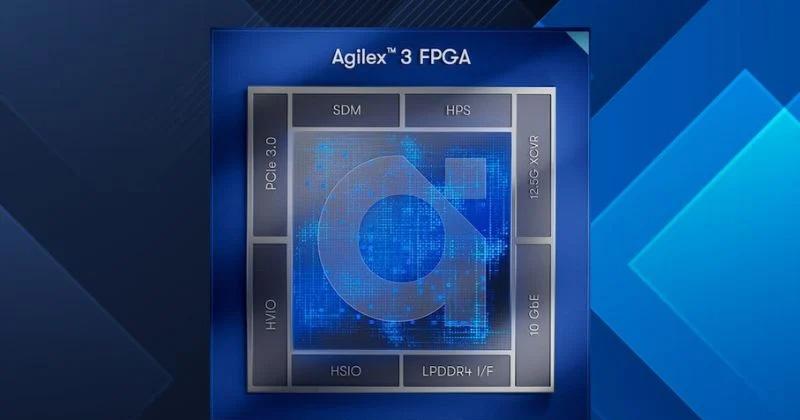
Microchip’s FPGAs Earn QML Class V for Space Missions
Microchip Technology Inc. announced that its radiation-tolerant (RT) RTG4 FPGAs, with lead-free flip-chip bumps, have achieved the highest level of space qualification—QML Class V status—designated by the Defense Logistics Agency (DLA). Microchip’s RTG4 FPGAs are now even more crucial for very demanding space missions, including human-rated, deep space and national security applications, where the highest dependability is absolutely vital.
The QML Class V certification for space components shows that the product has been extensively evaluated to meet the high performance and quality requirements set by the DLA. The consistent performance measurements of QML certifications help users have confidence in using these FPGAs for mission-critical designs while simplifying their own certification and design processes.
Rising to QML Class V certification in 2018, the RTG4 family became the first to include more than 150,000 logic pieces. By using lead-free, flip-chip bumps in its FPGAs, a method that guarantees improved product lifetime, Microchip has now increased the standard. The new lead-free bumps utilized in the RTG4 FPGAs satisfy all required DLA inspection requirements, including MIL-PRF-38535 criteria. Flip-chip bumps link the silicon die to the package substrate, and the lead-free bumps had no indications of tin whiskers—a typical problem causing component breakdown.
Lead-free, flip-chip technology
Minh Nguyen, technical staff engineer for Microchip’s FPGA business unit, underlined the developments in lead-free, flip-chip technology that differentiate Microchip’s RTG4 FPGA from rivals in the space industry.
“The RTG4 FPGA ceramic package has a unique hermetically sealed construction. The solder seam seal between the package lid and cavity walls prevents the ingress of moisture, debris and contaminants,” she said.
This design ensures long-term reliability for deep space missions, as the hermetic seal also serves as an electrical connection to ground. According to Nguyen, this eliminates the potential for floating components, which are a concern in harsh space environments.
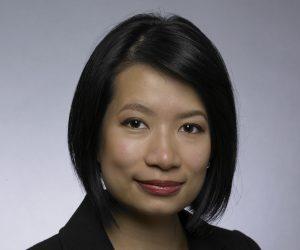
“Other FPGA competitors have ceramic packages,” she said. “But they are non-hermetic due to gaps between the package lid and substrate.”
These spaces can let pollutants in, causing internal decoupling capacitors and the die to corrode over time, therefore compromising dependability. By contrast, the architecture of the RTG4 allowed it to be qualified to QML Class V standards—a classification reserved for hermetic microelectronics.
Nguyen further underlined the significance of the sophisticated lead-free, flip-chip technology developed by Microchip.
“Flip-chip bumps are utilized to connect the silicon die and the package substrate. Critical for long-term space flights, the lead-free bump material we have chosen helps extend the lifetime of the product,” she said.
She also pointed out that the lead-free bump design let RTG4 pass rigorous dependability testing needed under MIL-PRF-38535 criteria, running up to 2,000 heat cycles from −65 degrees Celsius to 150 degrees Celsius. According to Nguyen, the lead-free, flip-chip bump interface connections passed MIL-PRF-38535 inspection criteria and exhibited no signs of tin whiskers.
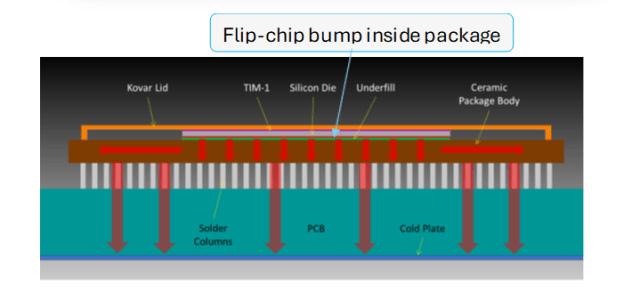
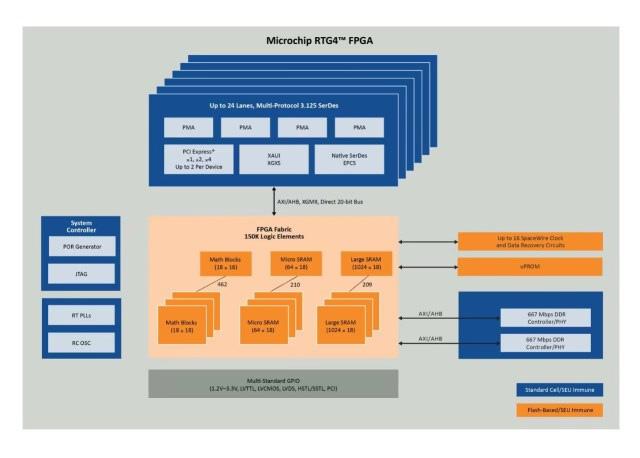
Technical challenges
Nguyen explained the key challenges in developing lead-free, flip-chip bumps for the RTG4 FPGAs and how Microchip overcame them to meet the stringent QML Class V standards.
“We aimed for QML Class V qualification, the highest level designated by the Defense Logistics Agency (DLA), which is essential for mission assurance in human-rated, deep space, and national security programs,” she said. To achieve this, Microchip needed to pass rigorous testing, including thermal cycling through extreme temperatures, thermal shock and high-temperature storage.
Nguyen noted that the original RTG4 FPGAs, featuring leaded flip-chip bumps, had already gained QML Class V qualification and a proven flight heritage. “We needed to ensure a smooth migration path for users adopting the lead-free version,” she added.
Fortunately, the lead-free, flip-chip bump is inside the FPGA package, making it a drop-in replacement. “There’s no impact on the user’s design, reflow profile, or thermal management when converting to the lead-free bump RTG4 FPGAs,” Nguyen said.
Nguyen further emphasized the impact of the QML Class V qualification on Microchip’s positioning in the space components market. “This milestone gives customers added confidence in using RTG4 FPGAs in space flight systems, while benefiting from high-reliability, zero-configuration-upset, and low-power features,” she said.
With over 60 years of experience in powering space missions, Microchip remains dedicated to product longevity and quality. “Because QML qualifications are standardized based on specific performance and quality requirements governed by the DLA, customers can streamline their design and certification processes by using QML-qualified products over commercial alternatives,” Nguyen added. ]”We have been able to offer a solution that not only improves dependability but also guarantees a longer product lifetime, essential for space exploration.”
Microchip’s approach to power efficiency, radiation tolerance and system-level integration has long set its space-grade FPGAs. One of the key differentiators is the company’s use of programming technologies that provide immunity to radiation-induced configuration upsets. “Our radiation-tolerant and commercial FPGAs are designed to avoid scrubbing and reloading the FPGA configuration,” Nguyen said. This feature not only reduces power consumption but also helps designers cut down on bill of materials costs and save board space, offering a streamlined solution in space electronics.
Power management is another critical factor in space systems, as satellites rely on limited power from solar panels that degrade over time due to radiation exposure. Excess heat is also a major challenge, as satellites in space cannot use traditional cooling methods like fans.
“Our programming technology gives us intrinsically low static power, which aids in managing thermal issues,” Nguyen said. Components that generate excessive heat can create costly thermal management problems, and Microchip’s FPGAs are specifically designed to mitigate this by minimizing heat generation.
Looking ahead, Microchip will continue focusing on future space applications, targeting both critical missions like deep space and human-rated programs, and more cost-sensitive missions like Low Earth orbit (LEO) satellite constellations. Nguyen noted that Microchip plans to evolve its space-grade FPGA portfolio over the next decade by tackling the ongoing challenges of power, radiation, reliability and security, while enhancing computing throughput.
Development kits, mechanical samples, and daisy chains packed for board validation and testing support the RTG4 FPGAs. Comprising a large IP library, full reference designs and development kits, Libero SoC Design Suite allows RTL access through programming.