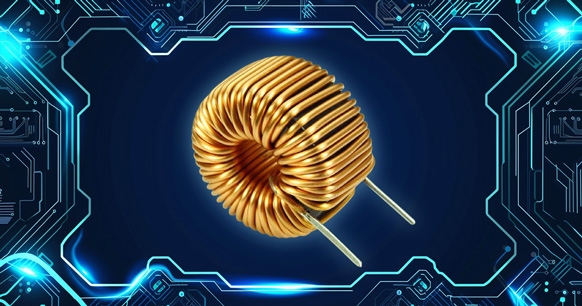
Essential Guide to Vibration Isolators: Types, Benefits, and Industrial Applications
A vibration isolator serves as an elastic connection between equipment and its foundation, with the purpose of reducing or eliminating the transmission of vibration forces from the equipment to the foundation, as well as from the foundation to the equipment. In this article, we will introduce you to some types of vibration isolators and their applications.
Digital Electronics: Optocoupler | Optoisolator - Driving a high-current CREE XLamp XR-C LED
Catalog
I. Types
1. Metal Rubber Vibration Isolator
2. Steel Spring Vibration Isolator
3. Rubber Vibration Isolator
II. Applications
1. Vibration Isolator Pad
2. Steel Vibration Isolation Base
I. Types
1. Metal Rubber Vibration Isolator
Metal rubber is a synthetic product designed to simulate the properties of natural rubber. The metal rubber component is constructed from metal wire and does not contain any natural rubber, yet it possesses the same elasticity and porosity as natural rubber. This makes it particularly well-suited for addressing challenges related to high and low temperatures, significant temperature variations, high pressure, and high vacuum environments.
The internal structure resembles a network, similar to the macromolecular structure of natural rubber. When subjected to alternating stress and strain, it effectively dissipates a large amount of vibration energy. This results in a significant increase in damping within the resonance zone, effectively suppressing resonance peaks.
In the vibration isolation zone, internal damping decreases rapidly, giving it excellent damping characteristics with a damping ratio ranging from 0.2 to 0.3.
The stiffness characteristic of metal rubber also exhibits a non-linear behavior, transitioning from linear-soft to characteristic-hard as the amplitude increases. This gradual softening of stiffness results in a reduction of the system's "natural frequency" in the spatial direction, providing effective vibration isolation as the external excitation magnitude increases. Metal rubber can be described as a material with loose structure, high elasticity, and excellent damping characteristics, with a density of only about 0.3 compared to metal.
Furthermore, metal rubber is capable of withstanding high temperature, high pressure, high vacuum, and ultra-low temperature environments without evaporation or fear of space radiation and particle impact. It has long storage and service life without any aging phenomenon. In contrast to natural rubber used in bridge damping bearings which has a working temperature range of -40°C to 60°C, metal rubber operates within an impressive range from -150°C to +360°C. These advantages are clearly evident when considering potential replacement costs and economic losses due to aging failures associated with natural rubber materials.
Overall, it is clear that metal rubber offers superior performance across various environmental conditions while maintaining longevity and reliability compared to traditional damping materials like natural rubber.
Hence, various components made of metal rubber not only function effectively in the challenging environments mentioned above, but also maintain exceptional properties under these conditions. They are able to meet the specific requirements of spacecraft for national defense and other specialized working environments, fulfilling the special needs for component materials.
Metal rubber vibration damping and isolation components are characterized by their compact size and lightweight nature. They can be crafted into a variety of vibration isolators, suitable for dampening vibrations and isolating electronic instruments, power equipment, and pipelines. Particularly well-suited for demanding environments such as aviation, aerospace, navigation, and the chemical industry.
2. Steel Spring Vibration Isolator
Steel spring isolators can be applied to a wide range of equipment, from heavy machinery to lightweight precision instruments. They are typically used in situations where the static compression exceeds 5 cm or when environmental factors such as temperature make it unsuitable to use rubber or other materials.
The benefits of using steel spring isolators include their ability to handle large static compression, low natural frequency, and effective isolation of low-frequency vibrations. They are also resistant to corrosion from oil, water, and solvents, and remain unaffected by changes in temperature. Additionally, they do not experience aging or creep and their characteristics remain consistent during mass production.
However, there are some drawbacks associated with steel spring isolators. They offer very little damping (with a damping ratio of about 0.005), resulting in high transmission rates at resonance. There is also a tendency for them to transmit vibrations along the steel wire at high frequencies and produce rocking motion without external damping mechanisms such as metal silk, rubber, or felt. Steel springs come in various shapes including spiral, disc, ring, and plate; with spiral springs being the most commonly used.
When considering the TJ1 spiral steel spring vibration isolator manufactured in China specifically: it has a load capacity ranging from 17 to 1020 kg and a natural frequency between 3.5 and2 .2 Hz ,as well as static compression within is20-52mmwhen under technology operations.
Overall, the steel hinge achieves its superior vibration compensation based on its biography.
3. Rubber Vibration Isolator
The main design parameters of rubber vibration isolators are determined by the type of rubber used in the isolators. They need to have good vibration isolation, buffering, and noise reduction capabilities, as well as stable performance and a long service life. It should be easy to shape as required and have strong adhesion to metal with a large area bearing capacity. Rubber isolators can withstand cutting, compressing, or cutting pressure but are rarely used for tension. Their advantage lies in their ability to be made into various shapes with different stiffness levels. Additionally, they have a greater internal damping effect compared to steel springs and can isolate excitation frequencies as low as about 10 Hz.
However, rubber isolators will age over time and exhibit greater creep under heavy loads (especially at high temperatures), so they should not undergo more than 10-15% continuous deformation through compression or 25-50% through shear.
Natural rubber has a slightly lower natural frequency than synthetic rubber. It has minimal changes in mechanical properties, high tensile strength, elongation when damaged is preferred for being cost-effective but cannot be used in contact with oils, hydrocarbons, or ozone at high equipment and ambient temperatures.
On the other hand: neoprene and nitrile rubber isolators provide good resistance against hydrocarbons and ozone; additionally nitrile rubber studs also better suit higher temperature environments.
Finally: silicone-rubber-based vibration isolation systems may prove optimal choice for very low OR very high (-75℃ TO +200℃) temperature working so much that other materials found unsuitable just cannot handle such extremes.
II. Applications
1. Vibration Isolator Pad
Vibration isolator pads come in a variety of materials, including cork, felt, rubber pads, and glass fiberboards. They offer several advantages: they are cost-effective, easy to install, and can be cut to the required size or overlapped to achieve different levels of vibration isolation. Metal rubber vibration isolator pads are made from metal wire and share the same elasticity and porosity as rubber. They are particularly well-suited for addressing challenges such as high or low temperatures, large temperature variations, high pressure or vacuum environments, strong radiation, severe vibrations, as well as damping and reducing vibrations. These pads can also be used for filtration, sealing, throttling noise absorption and reduction in corrosive environments. Additionally they can be customized into various shapes depending on specific working conditions. Furthermore these Metal rubber vibration isolator pads have a long shelf life without any aging issues making them an excellent substitute for regular rubber especially in aerospace applications national defense weaponry equipment civilian products..
It is my great honor to introduce the advantages of metal rubber vibration isolator pads:
1) The use of metal wire as raw material gives it the same elasticity and porosity as rubber, without containing any ordinary rubber.
2) It has the ability to resist high and low temperatures, large temperature differences, high vacuum, strong radiation, and corrosive environments.
3) With a high carrying capacity and fatigue resistance, it does not exhibit aging phenomenon, resulting in a long service life and storage time.
4) These pads can meet various needs such as damping, vibration reduction, sealing, filtering, throttling, sound absorption, and noise reduction. They are considered to be the best substitute for ordinary rubber products and other porous material products within special industrial and mining applications.
5) Its performance indicators can be customized through different process parameters and methods in order to prepare metal rubber products with different structural sizes and performance characteristics.
6) It is suitable for numerous fields such as aerospace industry,, missile ships,, starships,,, national defense weapons equipment,,, petrochemical industry,,and automobile industry--with distinctive features catering towards both military civilian use.
2. Steel Vibration Isolation Base
The machine is often installed on a vibration isolation base, typically made of concrete or steel. The use of heavy and rigid concrete inert blocks serves several functions:
1) Reduce vibration and minimize the impact of unbalanced forces from the machine;
2) Enhance force resistance and ensure secure installation of the machine;
3) Lower the center of gravity for increased stability;
4) Decrease the natural frequency.
Ideally, the weight of the inert block should be at least equal to that of the machine, preferably twice as much. For reciprocating engines and compressors, a base 3 to 5 times the weight may be necessary, while lighter machines might require a base up to 10 times their own weight.