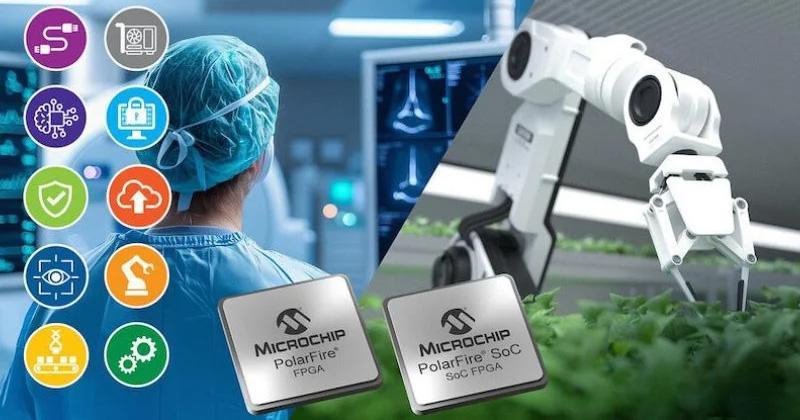
New Position Sensing ICs Simplify Design and Enhance Precision
Recent innovations in EVs and robotics have driven the demand for increasingly complex motion system designs. In this roundup, we explore how Allegro Microsystems, Melexis, and CambridgeIC are addressing this challenge with their latest sensor ICs to provide precise position-sensing solutions while also simplifying design and integration.
Allegro Microsystems Unveils Position-Sensing ICs
Allegro Microsystems revealed new inductive position sensors and micropower magnetic switches and latches at Electronica 2024. Allegro claims these new ICs can lower costs, extend battery life, and improve performance for motion systems in automotive, industrial, and consumer applications.
Allegro introduces advanced sensing products for automotive, industrial, and consumer applications. Image used courtesy of Allegro Microsystems
The inductive position sensors, A17802 and A17803, are compact alternatives to encoders and resolvers in position sensing. Their programmable linearity and digital compensation can increase accuracy and operate in extreme conditions, ranging from -40°C to 160°C. Developed per ISO 26262:2018 ASIL C and D (pending assessment), both of these sensors are designed for automotive applications as position sensors for motors in steering systems or pumps in thermal management systems. The A17802 provides analog outputs over differential sine and cosine, while the A17803 provides additional digital interfaces.
The newly announced APS11753 and APS12753 are micropower Hall-effect switches and latches. With ultra-low current consumption in the µA range, these ICs reportedly use 50% less power than Allegro’s existing micropower offerings. They feature flexible sleep mode options and built-in chopper stabilization to reduce offset drift. Additionally, they can operate from 2.2 V to 5.5 V without additional regulators and provide various magnetic sensitivity options to cater to flexible requirements.
The ICs are offered with and without AEC-Q100 qualification for stress testing. The APS11753 and APS12753’s low power advantages make them suitable for medical wearables such as hearing aids, smart home devices, or industrial remote monitoring systems.
Melexis Showcases Robotics Position-Sensing Tech
Melexis recently announced the MLX90384, an 18-bit angular encoder IC that will be the first product featuring Melexis’ new Arcminaxis technology. Historically, robotic design required a trade-off between performance and cost in position tracking solutions. Optical solutions offer high precision but are costly, while magnetic dipole-based solutions are more affordable at the cost of accuracy. Arcminaxis technology aims to bridge this gap by delivering magnetic sensors with better precision, making it a middle-ground solution for robotics and automation applications.
Functional block diagram of the MLX90384. Image used courtesy of Melexis (Link downloads datasheet as PDF)
The MLX90384 IC (link downloads datasheet as PDF) is a magnetic position sensor featuring an 18-bit resolution and a pitch-independent design that accommodates magnets of various sizes and pole pair configurations. This makes it highly adaptable to different magnet designs. The Arcminaxis technology provides features aimed at reducing design complexity. Its magnet-sensor tolerance of ±0.5 mm simplifies mechanical assembly. Its nominal air gap of 1.5 mm allows the sensor and magnet to be operated and mounted within a robotic joint safely. It also features multi-axis magnetic field sensing (axial and tangential), which eliminates the need for precise sensor placements.
Allegro claims these features help reduce sensor and magnet costs while minimizing design complexity by enabling easier assembly and integration. The MLX90384 is available as a four-component set consisting of the sensor IC, a Vernier-type magnet, a precompiled STM32-based software package, and a reference design for custom encoder solutions. An evaluation kit is also available for testing and development.
CambridgeIC Expands PCB-Based Precise Angle Encoder
CambridgeIC showcased its new CAM622 resonant inductive encoder ICs at SPS Nuremberg 2024. The CAM622 measures position through a sensing engine and generates encoder-style (ABN) outputs through its interface processor.
In the past, the sensors came in PCBs with etched coil patterns and used standard PCB fabrication methods. Targets, on the other hand, came in the form of PCBs with transponder coils that are harder to assemble and manufacture. Like other CambridgeIC processors, the CAM622 uses a specialized approach: the IC’s sensing engine connects to compatible "sensors" to perform angle measurements of a contactless rotating mounted "target." Both the sensors and targets are resonant inductive circuits embedded in a PCB.
CAM622’s function overview. Image used courtesy of CambridgeIC (Datasheet link downloads as a PDF)
CAM622 leverages rotating targets to use PCB coils. It accomplishes this by increasing operating frequency and tweaking the circuit’s quality factors. This means that the new Type-B sensors and Type-B targets can be manufactured using PCB fabrication techniques and assembled more quickly. The sensors and targets are designed symmetrically to reduce the need for precise alignment and come in outside diameters of 25 mm, 30 mm, and 50 mm. Customers can obtain Gerber files for the sensors and targets and manufacture parts themselves.
CAM622 also features an update to its interface processor. Compared to the previous CAM502, the CAM622 has an internal sample rate benchmark six times faster at 33,000 measurements per second. It works on an SPI interface primarily used for configuration and diagnostics of the ABN outputs that can double as an output interface. The CAM622 ABN board is available for evaluation and testing.
Position Sensors of the Future
The position sensors highlighted in this article reflect a growing trend toward position-sensing ICs that prioritize design simplicity while balancing precision with cost-effectiveness. This technology is crucial as motion systems in automotive and robotic industries have stricter requirements. By offering high performance at relatively lower costs, they are poised to play a key role in driving innovation in downstream applications across automotive, robotics, and industrial systems.